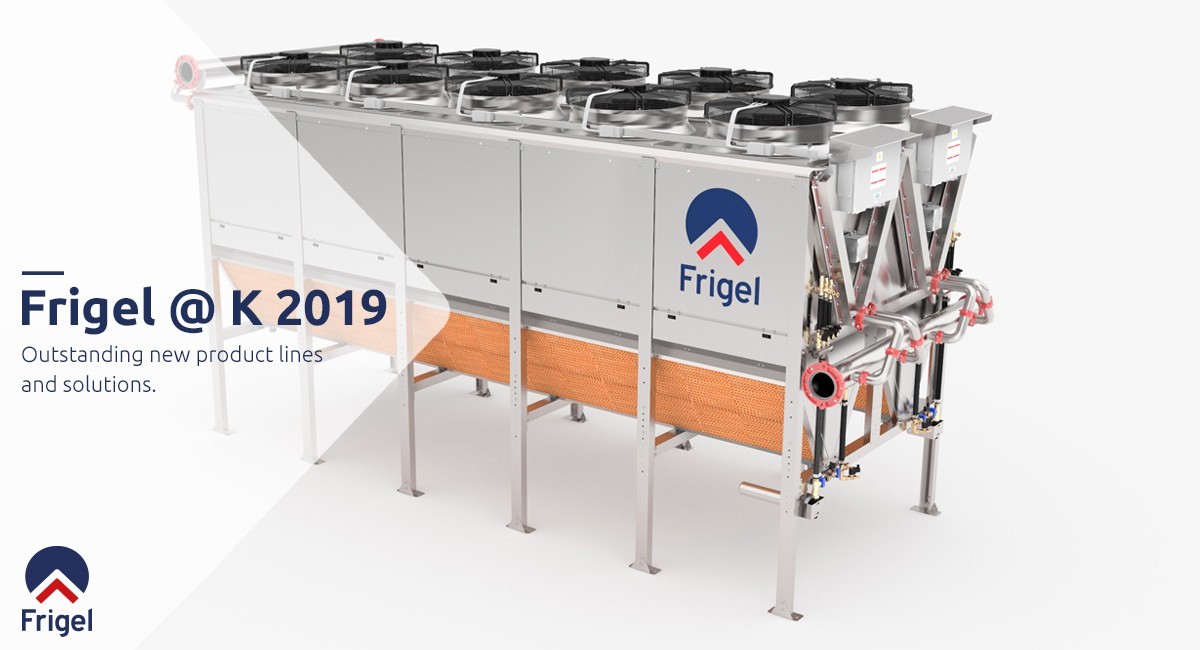
Frigel @K 2019
Outstanding new product lines and solutions for cycle time reduction and cost savings help plastics processors effectively compete and increase profitability.
Frigel will bring to the K Show in Germany a complete portfolio of the most advanced cooling solutions for the plastics industry. At the booth, visitors will have the opportunity to view the entire product line breadth, with special attention to all new developments, which include new full digital control technology and outstanding innovations and upgrades in almost all product categories. The highlights:
Ecodry – Adiabatic Fluid Cooler
Displayed at the booth, the latest upgrade of our internationally patented Ecodry System, the most proven adiabatic cooling technology in the market today that, thanks to its 95% water savings, has replaced, up to now, more than 8000 evaporative cooling towers worldwide. The unit will be presented in its glycol-free, self-draining configuration, with an inverter driven pumping station and new advanced digital control panel.
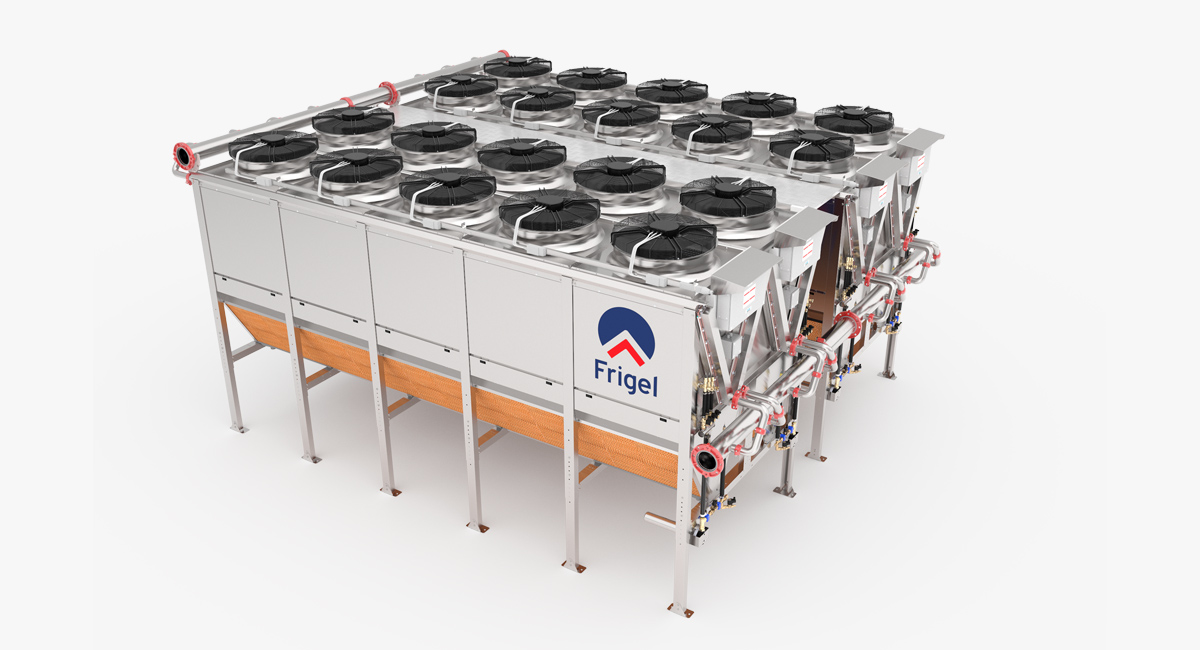
Microgel™ – TCUs with Booster Pumps and Integrated Portable Chiller
Frigel will be presenting also the traditional ranges of Microgel for Injection Molding (RCM/D Series) – single and dual zone, for molding throughputs from 10 to 900 kg/hr (20 to 2000 lb/hr) and Microgel for Packaging (RCP Series) – from 100 to 2000 kg/hr (220 to 4400 lb/hr), now both with 100% new digital technology and touch screen control.
With more than 40,000 units installed worldwide, these unique high-performance mold cooling units have provided real life cooling cycle time reductions (up to 50%), together with impressive part quality improvement through perfect mold temperature control and high energy savings, thanks to their unique automatic free-cooling feature. The new digital technology provides energy and flow monitoring and includes inverter driven booster process pumps.
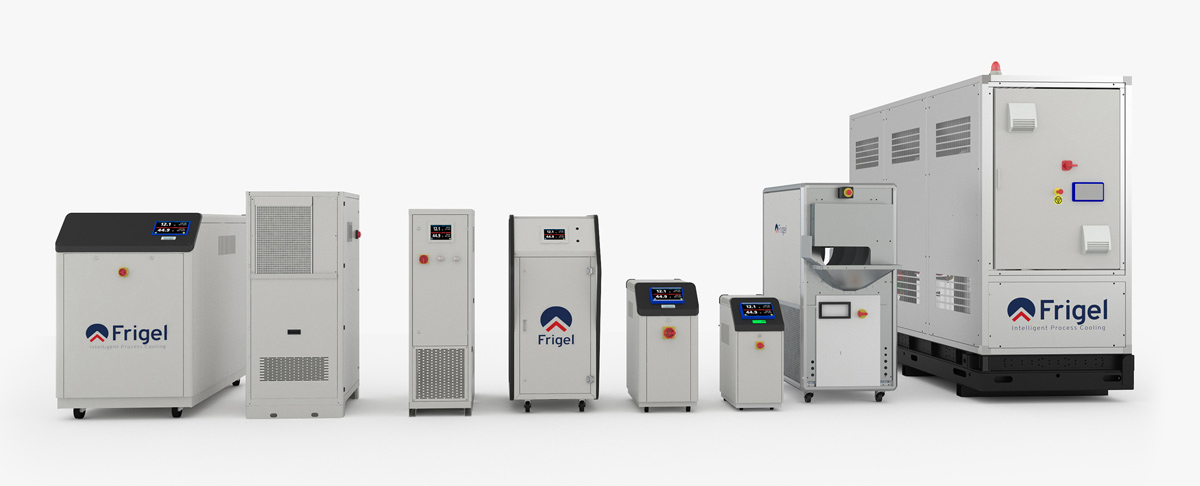
New Lines of Mold Temperature Control Units
Also engineering resin molders will find at our booth an impressive offering of mold temperature controllers for every possible application. Four completely new lines of Thermogel will be presented.
Starting with a new TBD Series – up to 90°C (194˚F) – offering a robust and cost effective solution for general molding applications. Then, the new TDK Series – up to 120°C (248˚F) and TPK Series – up to 180°C (356˚F) pressurized water TCUs for high temperature applications will be on display. This new line was recently developed and designed in a joint venture with Matsui – the Japanese leader in plastics technologies.
For those who might be looking for high-tech molding solutions, Frigel presents the new Thermogel Heat&Cool THC Series – process synchronized alternating heating and cooling units that work with pressurized water up to 180˚C (356˚F). These units are designed specifically for high quality surface finishing of molded parts.
Finally, a new Turbogel range – TGM/D Series – up to 90°C (194˚F) – a unique TCU featuring powerful booster pumps and high performance cooling capacity, specially designed for cycle time reduction in high throughput molding applications. This range presents a complete restyling and upgrade from the traditional series. The new digital control allows, also in this case, energy and flow monitoring and inverter driven booster process pumps.
New Central Chillers
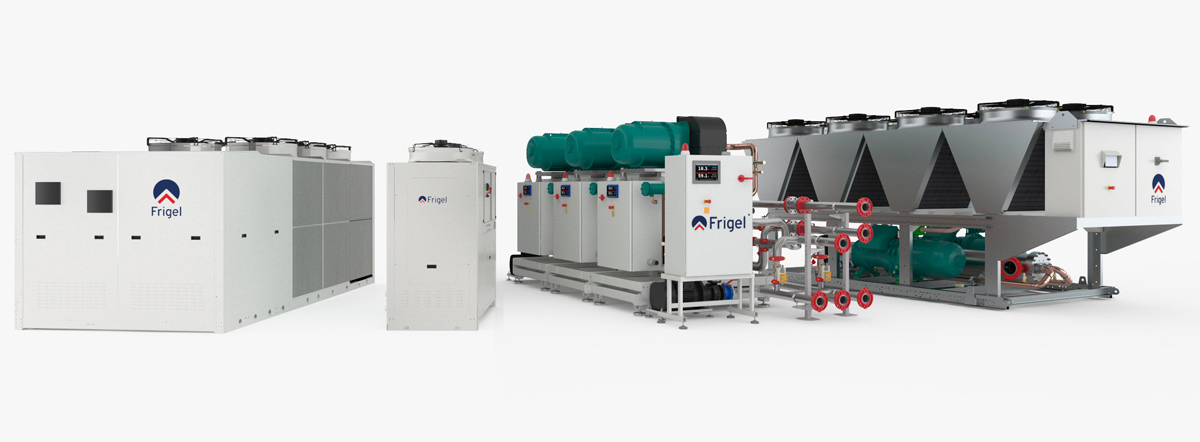
Two new lines of chillers will be presented to the plastic market for the very first time:
Our new IndustrialChiller – Air Cooled MRM Series – includes a full range of modular chillers from 90 to 580 kW (25.6 to 165 tons). This heavy-duty, industrial-grade new line is more efficient, reliable and cost effective than the previous Heavygel HGM. Featuring Multi-Scroll compressors, microchannel condensers and a wide range of options covering all process demands and extreme weather conditions, this new line offers the lowest Total Cost of Ownership (TCO) for this type of chillers in the market.
Another important innovation to be presented is the new ModularChiller – Water Cooled 3FX Series. These unique chillers combine high performance cooling capacity with unbeatable efficiency in self-contained packages with extremely small footprints. They are equipped with rotary (scroll or inverter driven screw) compressors and are specially designed to add capacity as the thermal loads increase, with system cooling capacities up to 3000 kW (850 tons).
New Solutions for Packaging
For Packaging applications, Frigel will be presenting two completely new products:
CapCooler – CAP Series – Post-molding closure cooling units for ultra-fast molding cycles.
MoldDryer – MDE Series – Air dehumidifiers for mold enclosures to avoid sweating in low cooling water temperature applications.
New Digital Factory Supervision System 4.0
MiND™ – An innovative digital solution developed by Frigel to meet the ever increasing needs of modern companies to reach Industry 4.0 and IIOT (Industrial Internet of Things) standards. MiND is able to provide customers a perfect supervision and maintenance tool for all Frigel equipment and accessories, both central and machine-side, allowing monitoring and management of all working parameters and events and registering performance and energy consumption of every single cooling system component through a multifunctional user interface, both locally and remotely, through a user-friendly webpage.
For more information
Contact us