Increased productivity in the packaging industry
Ecodry System 4.0
Process-Synchronized Cooling
Designed for increasing productivity in injection and blow molding of plastic packaging, thanks to the significant reduction in cooling time. It guarantees perfect stability, as well as considerable savings in operating costs and a reduction in environmental impact.
Ecodry 4DK
Adiabatic Cooling System
- Up to 15% less energy consumption
- Water saving up to 95%
- Safe operation without glycol down to an ambient temperature of -30 °C (-22 ˚F)
- Remote monitoring
- Improved COP up to 30%
Reduction of cycle time without waste
Microgel Injection Molding RCD
Temperature Control Unit with Chiller
- Control of the mold temperature synchronized with the process
- Cycle time reduction up to 25%
- Intelligent use of energy consumption
- Increase of productivity (up to +33%)
Efficient and economical production
Microgel Packaging RCP
High performance mold cooling unit
- Cooling synchronized with the process
- Cycle time reduction up to 30%
- High energy efficiency (pumps and compressors with inverter)
Productivity at the highest levels
Microgel Packaging RCP
High performance mold cooling unit
- Cooling synchronized with the process
- Cycle time reduction up to 30%
- High energy efficiency (pumps and compressors with inverter)
Productivity at the highest levels
Cap Cooler
Caps post-cooling unit
- Uniform cooling for each type of closure and adaptable to any production requirements
- Guarantees a consistent production rate and constant quality of the product
- Minimizes ovalization and deformation
Increase in production performance
Microgel Packaging RCP
High performance mold cooling unit
- Cooling synchronized with the process
- Cycle time reduction up to 30%
- High energy efficiency (pumps and compressors with inverter)
Increase in production performance
Mold Dryer
Industrial air dehumidifier
- Production released from climatic conditions with constant quality
- Reduced maintenance and long life for the molds
- High energy savings compared to traditional systems
Remote control platform
- Unique central inferface for control of the cooling system
- Easy visualization of the connected equipment
- Alarm management and history
- Multiple access levels
Machine Interactive Database
Supervision system for plant control and optimization
- Remote control of machines from everywhere
- Live data recording (all the operating parameters)
- Data stored locally, physically installed on-site
- Safe and encrypted Data transfer
Microgel Injection Molding RSD
Revolutionary Temperature Control Unit with Chiller
- Control of the mold temperature synchronized with the process
- Increased production up to 50% thanks to the drastic reduction of cooling time
- Intelligent use of energy consumption
- Affordable investment & high ROI
- It does not require modifications to the mold
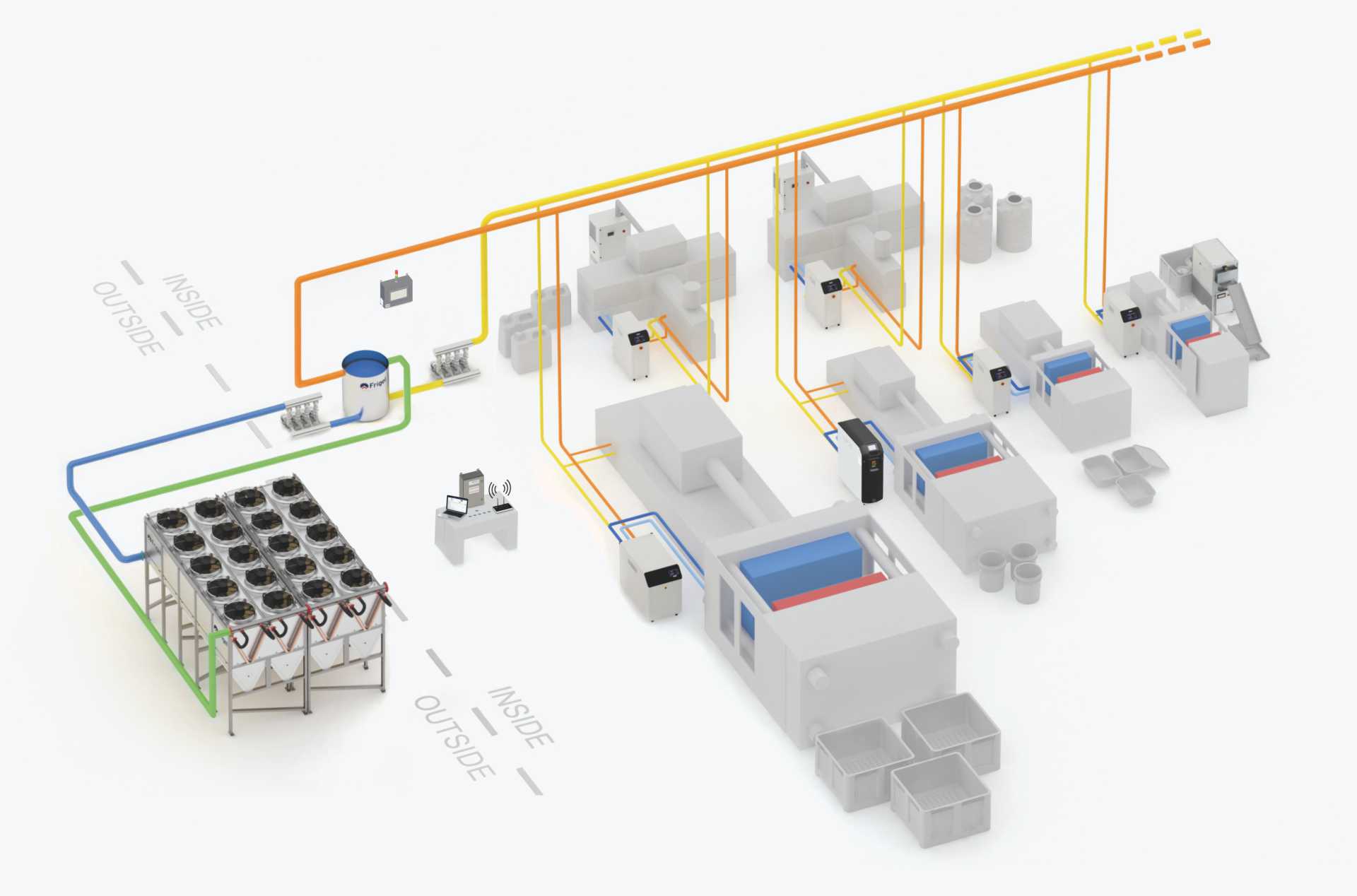
Download the brochure of the cooling system Packaging
Performance and sustainability without compromise
Increased productivity
1. Significant reduction in cooling times
Thanks to their ability to synchronize with the production line, the units can activate strong cooling, providing low temperatures and high flow rates to the mold, only during certain phases of the cycle.
2. Total control flexibility
Thanks to the wide range of units, even with built-in chiller (Microgel), there is no limit to the settings of the cooling or thermo-regulation temperature from 0 to 200 °C (30 to 400 ˚F) and of the flow rate in each circuit of the mold, for each type of application.
3. Perfect repeatability
Synchronization with the process ensures precise control of the mold temperature at every stage of molding, without interference, while the process machines operate constantly at maximum performance.
Reduced operating costs
1. Energy savings up to 30%
• Synchronized cooling - The units are activated automatically only when needed, achieving significant energy savings.
• Intelligent use of chilled water -
The integrated chillers will operate only where and when it is needed.
• Free-Cooling opportunities - The units with integrated chiller have the function of automatic Free-Cooling. Whenever the temperature required by the process is higher than the temperature supplied by the central system, the compressors stop.
2. Water savings up to 95%
The central adiabatic cooling system operates in a dry mode without water consumption almost all year, exploiting the ambient air to transfer the heat coming from the processes. Only during periods of extreme ambient temperatures above 30 °C (86 ˚F), the system uses a minimal amount of water in evaporative mode.
3. Up to 90% maintenance savings
The central adiabatic system is a closed circuit that allows excellent heat transfer with minimal maintenance.
Total modularity
1. Easily expandable at any time
The Ecodry System allows the installation of the exact capacity required at each stage of plant development.
2. Gradual implementation
Even in existing plants, installing additional units is very simple thanks to the functional and effective modularity design.
3. Exact quantification of costs by line and product
Each unit can measure and record the specific energy consumption for each product.
4. Total reliability
The extreme simplicity, reliability and redundancy of the components of the adiabatic cooling unit minimizes the possibility of plant shutdown due to failures of the cooling system, ensuring the continuity of production 24 hours a day.
Reduced carbon footprint
1. Intelligent electricity consumption
With minimal waste.
2. Maximum savings
Obtained thanks to automatic and independent Free-Cooling by process.
3. Possibility of reducing the consumption of natural gas
Thanks to the heat recovery of processes through heat pumps.
Minimized water footprint
Unlike traditional systems, such as the evaporative tower, this new heat dissipation technology consumes water only during periods of extreme environmental temperatures, reducing water consumption to a minimum.
Reduced risks of emissions
1. Low GWP refrigerant
The system uses a refrigerant gas with the lowest GWP available to date.
2. Risk of losses and emissions reduced to a minimum
In each unit the refrigerant gas is divided into small separate circuits, minimizing the risk of emissions in the event of leaks.
3. Without disposal of chemical additives
It does not require the disposal of chemical additives used for water treatment.
Other solutions for Packaging
Discover our alternatives
High performance for every process need.